19 марта 2021 года
Группа 312
Предмет :"Техника и технология полуавтоматической сварки в среде защитных газов "
Тема занятия :"Контроль качества основных и сварочных материалов"
Тема 4. Контроль основных и сварочных (вспомогательных) материалов
Контроль основных и сварочных (вспомогательных при пайке) материалов(входной контроль) выполняют перед допуском материалов в производство. При этом решаются следующие задачи:
1. Установление соответствия химического состава, структуры, геометрических размеров, состояния поверхности и свойств материала требованиям НТД.
2. Назначение соответствующей обработки материала, необходимой для улучшения его структуры и свойств и корректировка технологии изготовления изделий с целью предотвращения выполнения технологических операций, связанных с обработкой материалов, имеющих дефекты.
Входной контроль включает следующие этапы:
1. Проверка наличия сопроводительных документов (накладная, сертификат).
2. Проверка сохранности упаковки и наличие на ней этикеток.
3. Внешний осмотр и выявление поверхностных дефектов.
4. Для ответственных конструкций проведение пробной сварки (пайки) и испытание материала и соединений.
5. Сортировка и маркировка принятого материала.
По результатам контроля составляется приемочный акт, если материалы соответствуют НТД или рекламационный акт (претензия к заводу изготовителю), если материал не соответствует НТД.
Основной (паяемый) материал поступает в виде листа, прутка, профиля, штамповки. В начале проверяют сертификат, в котором указываются марка, химический состав, номер стандарта, вид полуфабриката, свойства. После контроля сертификата основной материал подвергают внешнему осмотру с целью выявления трещин, расслоений, коррозии, вмятин, рисок и др. дефектов, связанных с отливкой слитка и его последующей обработкой давлением. Грубые дефекты выявляются визуально и мелкие – методами неразрушающего контроля. Проверяемый материал подвергают пробной сварке (пайке), которая проводится на образцах свидетелях с обеспечением их геометрического и технологического подобия реальным изделиям. Затем сварные (паяные) соединения подвергают механическим испытаниям, химическому, спектральному, металлографическому анализу и т.д.
Основной материал хранят в закрытых помещениях на стеллажах или в штабелях.
Сварочные электроды выпускают партиями, упакованными в пачки. Партия имеет сертификат. На упаковке имеется этикетка. После контроля сертификата и этикетки контролируют поверхность электрода на наличие трещин, сколов покрытия, пор и др., причем на каждый из дефектов есть нормы бракования. Электрод проверяют на прочность путем изгиба или падения с определенной высоты на пол. Проверяют покрытие на влагостойкость (после пребывания в воде), контролируют разнотолщинность покрытия по длине электрода.
При пробной сварке оценивают легкость зажигания дуги, стабильность её горения, равномерность плавления покрытия, отделимость шлака и т.д. После сварки соединения разрушают и осматривают изломы, проводят химический и металлографический анализ.
Проконтролированные электроды хранят в герметичных контейнерах или пеналах, так как нельзя оставлять электроды на открытом воздухе. При длительном хранении электродов контролируют параметры режима просушки.
Сварочную проволоку поставляют в бухтах или катушках, снабженных металлическими бирками. После контроля сертификата и бирки проволока поступает на очистку (механическую или химическую). После очистки проволока наматывается на кассеты. При намотке осуществляется контроль за состоянием поверхности проволоки. После выполнения пробной сварки осуществляют испытания и исследования сварных соединений. Проконтролированную проволоку хранят в герметичной упаковке. Время хранения контролируется.
Аналогично сварочной проволоке контролируют припой, который относится к вспомогательным материалам, используемым при пайке.
Сварочный флюс упаковывают в герметичные мешки, имеющие этикетки. После контроля сертификата и этикеток флюс контролируют на размер зерна путем просеивания через сито с ячейками, соответствующему верхнему и нижнему приделам размера зерна. Это называется гранулометрическим анализом. Далее флюс проверяют на содержание влаги путем просушивания и взвешивания. Флюс проверяют внешним осмотром на наличие инородных частиц.
После выполнения пробной сварки контролируют отделимость шлаковой корки, а при необходимости и механические свойства и химический состав наплавленного металла. После контроля флюс хранится в герметичных емкостях и периодически подвергается просушиванию.
Контроль флюса для пайки осуществляют аналогичным образом.
Защитный газпоставляют в баллонах, снабженных этикетками. После проверки этикетки на наличие примесей, газ контролируют на наличие влаги путем подачи струи на фильтровальную бумагу. При наличии влаги газ пропускают через осушитель, заполненный силикагелем. Для осушки аргона используется нагретая титановая стружка. При изготовлении особо ответственных конструкций защитный газ контролируют на химический состав.
Тема 5. Контроль технологического процесса сварки (пайки)
Контроль технологического процесса - это система операционного технического контроля, который включает контроль подготовки поверхности, сборки, процесса сварки (пайки) и при необходимости подварки (подпайки) полученных соединений.
Контроль подготовки поверхности перед сваркой включает осмотр лицевой и обратной поверхностей, которые должны быть зачищены до металлического блеска от загрязнений, смазки, ржавчины, окалины на ширину до 20-30 мм от стыка. Обработку производят как механическими, так и химическими способами. В ответственных конструкциях контроль подготовки осуществляют с белых бязевых салфеток. Особый контроль уделяют торцевым кромкам. Время хранения подготовленных к сварке деталей контролируется.
Перед контактной сваркой контроль качества подготовки поверхности осуществляют путем измерения электрического контактного сопротивления свариваемых деталей.
Контроль подготовки поверхности деталей перед пайкой аналогичен.
Контроль торцевых кромок толстостенных сварных конструкций включает проверку формы и геометрических параметров разделки (угол скоса и величина притупления кромки), которые называются конструктивными элементами свариваемых кромок. Размерный контроль осуществляют с помощью измерительных инструментов и шаблонов сварщика.
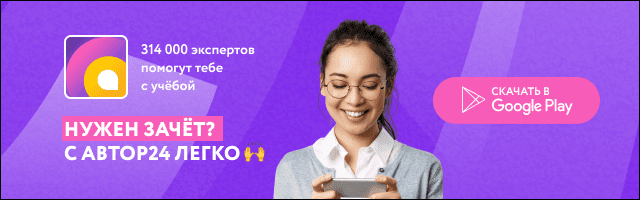
Контроль сборки включает операций контроля разметки и установки свариваемых (паяемых) деталей в соответствующее положение. Например, при сварке (пайке) нахлесточных соединений контролируют ширину нахлестки. При дуговой сварке стыковых соединений контролируют разметку начала и конца шва с целью последующей отрезки входных и выходных участков. При сборке стыковых сварных (паяных) соединений контролируют сборочные зазоры и смещения кромок.
При сборке высокоответственных стыковых соединений контролируют точность установки технологических планок, с которых начинается и заканчивается сварка. При сборке деталей типа «тела вращения» контролируют их соосность. При сборке тавровых соединений контролируют перпендикулярность свариваемых (паяемых) деталей.
Во всех случаях контроль сборки осуществляют в соответствии с чертежом изделия и выполняют с помощью шаблонов сварщика или измерительных инструментов.
Непосредственно перед автоматической дуговой сваркой проверяют правильность совмещения стыка свариваемых деталей с осью сварочной горелки.
При необходимости сборка перед сваркой заканчивается прихваткой, выполняемой отдельными точками или короткими швами. Контроль прихваток включает контроль длины прихваточных швов или диаметр прихваточных точек, их количества, шаг между ними, состояние поверхности прихваток и последовательность их постановки. Для отработки параметров режима прихватки её выполняют на технологических образцах с контролем геометрических размеров по шлифам прихваточных точек.
Контроль процесса сварки включает визуальное наблюдение за процессом плавления металла и формирования шва. Контроль параметров режима выполняют по показаниям контрольно-измерительных приборов. При сварке ответственных конструкций ведут непрерывную запись параметров. При двусторонней или многопроходной сварке обязателен контроль первого или корневого шва. Контролируют порядок наложения швов, количество проходов и слоев. Контролируют состояние поверхности каждого слоя после зачистки, время перерывов между проходами, последовательность выполнения швов.
Контроль процесса пайки предусматривает контроль температуры и времени пайки.
При обнаружении в швах недопустимых дефектов производят их механическую доработку и подварку (подпайку). Например, выполняют слесарную операцию по зачистке сварных швов от избыточных проплавов и околошовной зоны от поверхностного окисления.
Контроль подварки включает контроль правильности разметки дефектного участка. После разметки контролируют форму и геометрические размеры разделки (выборки) дефектного участка шва, выполненной механическим способом. Контролируют поверхность разделки, особенно на наличие острых углов, последовательность наплавки слоев, количество подварочных участков, их суммарную длину.
При обнаружении дефектов в паяных швах производят их подпайку, используя дополнительно припой. После подпайки производят внешний осмотр галтели.
Комментариев нет:
Отправить комментарий