01 февраля 2022 года
Группа 410
Предмет :"Основы электротехники"
Тема занятия :"Источники и приемники электрической энергии"
Источниками электрической энергии являются устройства (гальванические элементы, аккумуляторы, термоэлементы, генераторы), в которых происходит процесс преобразования химической, молекулярно-кинетической, тепловой, механической или другого вида энергии в электрическую.
31 января 2022 года
Группа 410
Предмет :"Основы электротехники"
Тема занятия :"Характеристика электрической цепи"
Параметрами электрической цепи являются R, L, C R - сопротивление L - индуктивность C – емкость. Любой элемент электрической цепи обладает сопротивлением, емкостью и индуктивностью. Это неотъемлемое свойство как цвет, вес, и т.п. Любая электрическая цепь, даже простейшая, обладает сопротивлением, емкостью и индуктивностью, поэтому параметры цепи – это ее сопротивление, индуктивность и емкость.
31 января 2022 года
Группа 410
Предмет :"Основы электротехники"
Тема занятий :"Постоянный ток"
Постоянный ток - общие понятия, определение, единица измерения, обозначение, параметры
Постоянный ток — электрический ток, не изменяющийся по времени и по направлению. За направление тока принимают направление движения положительно заряженных частиц. В том случае, если ток образован движением отрицательно заряженных частиц, направление его считают противоположным направлению движения частиц.
Строго говоря, под "постоянным электрическим током" следовало бы понимать "электрический ток постоянный по величине", соответственно математическому понятию "постоянная величина". Но в электротехнику этот термин был введен в значении "электрического тока, постоянного по направлению и практически постоянного по величине".
Под "практически постоянным по величине электрическим током" понимают ток, изменения которого во времени столь незначительны по величине, что при рассмотрении явлений в электрической цепи, по которой проходит такой электрический ток, этими изменениями вполне можно пренебречь, а следовательно, можно не учитывать ни индуктивности, ни емкости электрической цепи.
Наиболее распространенные источники постоянного тока — гальванические элементы, аккумуляторы, генераторы постоянного тока и выпрямительные установки.
В электротехнике для получения постоянного тока используют контактные явления, химические процессы (первичные элементы и аккумуляторы), электромагнитное наведение (электромашинные генераторы). Широко применяется также выпрямление переменного тока или напряжения.
Из всех источников э. д. с. химические и термоэлектрические источники, а также так называемые униполярные машины являются идеальными источниками постоянного тока. Остальные устройства дают пульсирующий ток, который при помощи специальных устройств в большей или меньшей мере сглаживается, лишь приближаясь к идеальному постоянному току.
Для количественной оценки тока в электрической цепи служит понятие силы тока.
Сила тока — это количество электричества Q, протекающее через поперечное сечение проводника в единицу времени.
Если за время I через поперечное сечение проводника переместилось количество электричества Q, то сила тока I=Q/t
Единица измерения силы тока — ампер (А).
Плотность тока — это отношение силы тока I к площади поперечного сечения F проводника - I/F. (12)
Единица измерения плотности тока — ампер на квадратный милл
В замкнутой электрической цепи постоянный ток возникает под действием источника электрической энергии, который создает и поддерживает на своих зажимах разность потенциалов, измеряемую в вольтах (В).
Зависимость между разностью потенциалов (напряжением) на зажимах электрической цепи, сопротивлением и током в цепи выражается законом Ома. Согласно этому закону для участка однородной цепи сила тока прямо пропорциональна значению приложенного напряжения и обратно пропорциональна сопротивлению I = U/R,
где I — сила тока. A, U— напряжение на зажимах цепи В, R — сопротивление, Ом
Это самый важный электротехнический закон. Подробнее о нем смотрите здесь: Закон Ома для участка цепи
Работу, совершаемую электрическим током в единицу времени (секунду), называют мощностью и обозначают буквой Р. Эта величина характеризует интенсивность совершаемой током работы.
Мощность P=W/t= UI
Единица измерения мощности - ватт (Вт).
Выражение мощности электрического тока можно преобразовать, заменив на основании закона Ома напряжение U произведением IR. В результате получим три выражения мощности электрического тока P = UI= I2R= U2/R
Большое практическое значение имеет то, что одну и ту же мощность электрического тока можно получить при низком напряжении и большой силе тока или при высоком напряжении и малой силе тока. Этот принцип используют при передаче электрической энергии на расстояния.
Ток, протекая по проводнику, выделяет теплоту и нагревает его. Количество теплоты Q, выделяющейся в проводнике определяют формулой Q = I2Rt.
Эту зависимость называют законом Джоуля-Ленца.
Смотрите также: Основные законы электротехники
На основании законов Ома и Джоуля-Ленца можно проанализировать опасное явление, которое часто возникает при непосредственном соединении между собой проводников, подводящих электрический ток к нагрузке (электроприемнику). Это явление называют коротким замыканием, так как ток начинает протекать более коротким путем, минуя нагрузку. Такой режим является аварийным.
На рисунке приведена схема включения лампы накаливания EL в электрическую сеть. Если сопротивление лампы R — 500 Ом, а напряжение сети U = 220 В, то ток в цепи лампы будет I = 220/500 = 0,44 А.
Схема, поясняющая возникновение короткого замыкания
Рассмотрим случай, когда провода, идущие к лампе накаливания, соединены через очень малое сопротивление (Rст - 0,01 Ом), например толстый металлический стержень. В этом случае ток цепи, подходя к точке А, будет разветвляться по двум направлениям: большая его часть пойдет по пути с малым сопротивлением — по металлическому стержню, а небольшая часть тока Iл.н — по пути с большим сопротивлением — лампе накаливания.
Определим ток, протекающий по металлическому стержню: I = 220/0,01 =22 000 А.
При коротком замыкании (к.з) напряжение сети будет меньше 220 В, так как большой ток в цепи вызовет большую потерю напряжения, и ток, протекающий по металлическому стержню, будет несколько меньше, но тем не менее во мною раз превышать ток, потреблявшийся ранее лампой накаливания.
Как известно, в соответствии с законом Джоуля-Ленца ток, проходя по проводам, выделяет теплоту, и провода нагреваются. В нашем примере площадь поперечного сечения проводов рассчитана на небольшой ток 0,44 А.
При соединении проводов более коротким путем, минуя нагрузку, по цепи будет протекать очень большой ток - 22000 А. Такой ток вызовет выделение большого количества теплоты, что приведет к обугливанию и возгоранию изоляции, расплавлению материала проводов, порче электроизмерительных приборов, оплавлению контактом выключателей, ножей рубильнике и т. п.
Источник электрической энергии, питающий такую цепь, может быть поврежден. Перегрев проводов может вызвать пожар. Вследствие этого при монтаже и эксплуатации электрических установок, чтобы предупредить непоправимые последствия короткого замыкания, необходимо соблюдать следующие условии: изоляция проводов должна соответствовать напряжению сети и условиям работы.
Площадь поперечною сечения проводов должна быть такой, чтобы нагревание их при нормальной нагрузке не достигало опасного значения. Места соединений и ответвлений проводов должны быть качественно выполнены и хорошо изолированы. В помещении провода должны быть проложены так, чтобы они были защищены от механических и химических повреждений и от сырости.
Чтобы избежать внезапного, опасного увеличения тока в электрической цепи при коротком замыкании, ее защищают с помощью предохранителей или автоматических выключателей.
Существенный недостаток постоянного тока состоит в том, что его напряжение сложно повысить. Это затрудняет передачу электрической энергии на постоянном токе на большие расстояния.
Смотрите также: Что такое переменный ток и чем он отличается от тока
28 января 2022 года
Группа 410
Предмет :"Техническая механика"
Тема занятия :"Сварные соединения ,способы сварки"
Виды сварных соединений и швов
Нередко причиной брака у начинающих сварщиков становится неправильно выбранные сварные соединения. Что неудивительно, так как со дня проведения первой сварки было разработано больше сотни разновидностей. В них несложно разобраться, поскольку сварные швы и соединения объединены в несколько групп по технике выполнения, положению деталей и другим признакам.
Содержание [Скрыть]
Что такое сварочное соединение
Новички ошибочно полагают, что понятия сварной шов и соединение равноценны. На самом деле шов ― это место стыковки двух заготовок расплавленным металлом с последующим охлаждением. Сварное соединение ― это три участка, которые подверглись действию высокой температуры. К ним относят:

Важно не путать два абсолютно разных понятия — сварочный шов и сварное соединение!
Сварочный шов ― это место стыковки двух заготовок расплавленным металлом с последующим охлаждением. Сварное соединение ― это три участка, которые подверглись действию высокой температуры.
Виды сварных соединений
В зависимости от того как расположены заготовки между собой к основным видам сварочных соединений относят:
Стыковые
Самые простые по выполнению швы даже для начинающих сварщиков. Ими соединяют заготовки, примыкающие друг к другу торцами, размещенные в одной плоскости или на ровной поверхности. При сварке деталей с разной толщиной допускается смещение поверхностей. Стыковым способом сваривают конструкции из листового проката, резервуары, трубы. Сравнительно с другими сварными соединениями сокращаются сроки выполнения работы и расход материалов, но нужно тщательно подготавливать кромки.
Угловые
Это сварные соединения двух металлических деталей под любым углом. Если заготовки разной толщины, толстостенную размещают снизу, чтобы на тонкой не появились прожиги и подрезы, сварочную ванну создают за счет плавления металла толстой заготовки. Для повышения прочности соединения швы накладывают с обеих сторон. Внутренний угол сваривают малым током, чтобы снаружи не образовалось закругление.
Угловые сварные соединения удобно выполнять способом «в лодочку». Заготовки прихватывают под нужным углом, затем устанавливают так, как будто это плывущий кораблик. После расплавления металл будет равномерно растекаться по обеим сторонам без образования дефектов.
Угловым способом сваривают каркасы небольших строений, емкости, навесы, кузова грузовиков. Кроме этого устанавливают детали конструкций в труднодоступных местах.
Нахлесточные
Такими сварными швами соединяют параллельно расположенные металлические пластины, которые наложены одна на другую с небольшим перекрытием. Для повышения прочности на разрыв и предотвращения проникновения влаги внутрь сварку выполняют с обеих сторон. Этим способом можно соединять листы толщиной до 12 мм. Для выполнения нахлесточных соединений от сварщика не требуется высокая квалификация, так как нет опасности прожога и не нужно подготавливать кромки. Недостатком считают повышенный расход металла.
Тавровые
Это сварное соединение торца одной детали с боковой поверхностью другой под прямым или небольшим углом. Если толщина заготовки больше 4 мм сварка проводится с обеих сторон с тщательной подготовкой кромок вертикальной пластины. Тавровые соединения применяют преимущественно при сборке несущих конструкций. Поэтому, если есть возможность изменения положения, сварку ответственных узлов лучше выполнять «в лодочку».
Торцевые
При выполнении таких соединений сваривают торцы заготовок, которые плотно примыкают одна к другой или расходятся от места стыка под углом не больше 30⁰. Способ применяют при производстве кожухов, вентиляционных коробов, контейнеров, металлических шкафов и пр. К достоинствам торцевого типа сварочных соединений относят низкую вероятность образования прожогов и внутренних напряжений, вызывающих деформацию. Недостатками считают завышенный расход материала и появление коррозии при проникновении воды между листами через дефекты шва.
Выбор сварного соединения зависит от расположения заготовок относительно друга друга.
Классификация сварных швов
Даже в одном типе соединения сварочные швы могут отличаться по конфигурации, протяженности, технологии и т. д. Поэтому в нормативных документах они сгруппированы по параметрам.
По положению в пространстве
По пространственному положению сварные швы могут быть:
По конфигурации
В эту группу занесены три вида сварочных швов, которые зависят от формы стыков. Они бывают прямолинейными, криволинейными, кольцевыми (спиральными). Конфигурация швов не зависит от пространственного положения заготовок.
По степени выпуклости
По форме поперечного сечения сварные швы квалифицируют как:
По протяженности
В эту классификацию входят сплошные и прерывистые сварные швы, которые выполняют отрезками по 10 — 30 см, но учитывается суммарная протяженность соединения. По расположению отрезков сварки прерывистые типы называют:
В зависимости от длины сварные швы относят к трем категориям:
По количеству проходов
Независимо от типа сварочные швы выполняют одним или несколькими проходами. Выбор варианта определяется толщиной металла и необходимой прочностью. При каждом проходе наплавляется один валик. Если их расположить на одном уровне образуется слой сварного шва.
Детали толщиной до 5 мм соединяют однопроходными швами. Угловые соединения из заготовок со стенками 6 — 8 мм сваривают одним слоем, а стыковые двумя. Многослойные швы используют при работе с толстостенными элементами и для предотвращения термических деформаций.
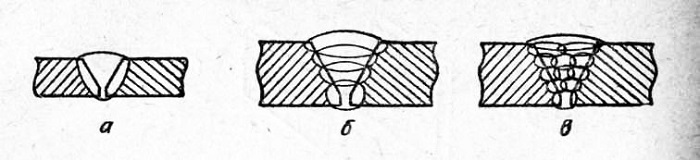
По направлению действующего усилия и вектору действия внешних сил
По этим критериям соединения и швы подразделяются на 4 вида:
По виду сварки
Классификацию по этому критерию проводят по типу сварочного аппарата, который создает условия для выполнения сварки. Из длинного списка технологий можно выделить основные виды;
Требования к сварным швам
Требования к швам зависят от условий эксплуатации, видов нагрузки, свойств металла, технологии сварки и пр. Для их классификации по конкретным условиям были разработаны ГОСТы. Например, требования к соединениям ручной сварки приведены в ГОСТ 5264-80.
К общим для всех швов независимо от условий относят:
Чтобы шов был качественным, необходимо соблюдать технологию подготовки металла и выполнения сварки.
О длине и толщине швов в зависимости от особенностей конструкции и марки металла, методах проверки качества и т. д. можно узнать из тематических СНиПов, которые нетрудно найти в свободном доступе. Полученные сведения можно использовать как шпаргалку при выполнении сложной работы.
27 января 2022 года
Группа 410
Предмет :"Техническая механика"
Тема занятия :"Виды, назначение и устройство цепных передач"
Устройство и принцип работы
Устройство цепной передачи очень похоже на конструкцию зубчатого привода. Но зубья ведущей и ведомой шестеренок не входят в непосредственное зацепление, а крутящий момент передается с одной на другую с помощью закольцованной непрерывной цепи, чьи отверстия надеваются поочередно на зубья вращающихся колес.
Цепная передача способна передавать вращение на параллельный ведущему вал, отстоящий от него до 7 метров. Она обладает рядом достоинств и недостатков по сравнению со своим прообразом.
Общие сведения о цепных передачах
Среди разнообразных приводов цепной считают относящимся к передачам с гибкой связью. Зацепление в ней осуществляется с помощью натяжения сочлененных звеньев бесконечной цепи. Она же передает и мощность от ведущего вала к ведомому. Из общих сведений о цепных передачах следует упомянуть следующее:
- КПД цепной передачи доходит до 90-98 %;
- передаточное число цепной передачи достигает 1:6;
- мощность на валу ограничена 120 кВт.
Передаточное отношение для цепной передачи рассчитывается по тем же формулам, что и для зубчатой. Изготавливаются цепные приводы из высокопрочных сортов стали, шестерни иногда делают текстолитовые или из полиамидных пластиков.
Классификация
Основная классификация цепных передач проводится по признаку использованной цепи. Выделяют:
- Роликовые. Контакт звена и шестерни осуществляется посредством ролика, одновременно скрепляющего звенья.
- Втулочные. Контакт идет посредством втулки, вращающейся вокруг ролика. Такое решение повышает ресурс цепного привода, но одновременно растут его вес и себестоимость.
- Зубчатые. Набираются из шарнирно сочлененных пластин, на внутренней стороне которых имеются профилированные впадины под зубья.
Кроме того, по числу насаженных на вал зубчатых колес и, соответственно, числу параллельных рядов в одном звене, различают такие виды, как:
- однорядные;
- двухрядные;
- многорядные.
Увеличение числа шестерен используется для повышения мощности либо для уменьшения габаритов изделия.
Достоинства
Относительно зубчатой можно сформулировать следующие достоинства цепной передачи:
- способность передавать крутящий момент да расстояние до 7 метров;
- частично гасить усилия, вызываемые изменением режима вращения.
По сравнению ременными передачами выделяют такие достоинства цепных, как:
- компактность;
- больший передаваемый момент при равных габаритах;
- стабильность передаточного числа, отсутствие пробуксовок.
Общим преимуществом цепных приводов считается их отказоустойчивость при частых разгонах и остановках.
Недостатки
К недостаткам цепных передач относятся следующие:
- высокая шумность, обуславливаемая постоянными соударениями деталей привода;
- скорый износ шарнирных сочленений, потребность в постоянной смазке и закрытом картере;
- растяжение по мере износа шарнирных сочленений;
- менее плавная передача вращения, чем у зубчатых приводов.
Для определенных сфер применения достоинства данного типа привода существенно перевешивают его недостатки
Сфера использования
Область применения цепных передач очень широка. Они традиционно используются в таких отраслях, как:
- транспорт;
- технологические установки;
- станочное оборудование;
- горная и дорожная техника;
- сельхозмашины.
Применение такого привода целесообразно при скоростях менее 15 метров в секунду, что ограничивает использование его в высокоскоростных приводах.
Приводные цепи
Приводы с зубчатой цепью используются в относительно медленных передачах. Для быстроходных механизмов используются роликовые и втулочные подвиды.
Цепной передачей служит и механизм подъема судовых якорных цепей, и подъемное оборудование — блок или полиспаст.
В этих механизмах цепь не имеет фиксированной длины, она изменяется по мере подъема (или горизонтального перемещения) груза. я
Роликовые приводные цепи
Роликовый подвид состоит из пары параллельных рядов боковых пластин, и осей, опрессованных в отверстиях наружных пластин. Оси проходят через втулки, которые, в свою очередь опрессованы в отверстиях внутренних пластин. На втулки надевают скользящие по ним ролики, а торцы осей расклепаны с формирование упоров, не дающим пластинам уходить вбок.
Ось поворачивается внутри втулки, создавая таким образом шарнирное сочленение. Ролик в момент зацепления катится по зубцу шестеренки, вращаясь на оси. Это выравнивает нагрузку от зубца и снижает износ элементов привода. Такие конструкции позволяют развивать скорость до 20 м/с
Втулочные приводные цепи
Втулочные конструкции лишены роликов, и по зубцу перекатывается сама втулка. Такое решение позволяет существенно снизить сложность, себестоимость и массу изделия, ни неминуемо повышает скорость его износа. Такие конструкции применяют для сравнительно тихоходных приводов (до 1 м/с), предающих ограниченную мощность.
Если же мощность требуется нарастить, на помощь конструкторам приходят многорядные цепи. параллельно расположенные звездочки меньшего размера дают возможность выбрать меньший шаг, понизить динамические усилия при разгоне и торможении валов. Скорость может достигать 10 м/с.
Мощность передачи при неизменном диаметре колес возрастает пропорционально их числу.
Сращивание концов при четном числе звеньев проводится звеном обычной формы. Если же число нечетное, то для сращивания приходится использовать особые переходные пластины, дважды изогнутые в плоскости вращения. Прочность этого звена получается значительно ниже, чем стандартного, поэтому конструкторы стараются избегать таких решений.
Зубчатые приводные цепи
Такие цепи в каждом своем звене имеют ряд пластин в выточенными (или отштампованными) на них парой зубьев, совпадающими по модулю с зубцами звездочек. Между зубцами на пластине выполнена впадина, соответствующая по форме зубцу. Пластины входят в зацепление с зубцами и передают энергию вращения. Звенья оснащают шарнирами трения качения — вращающимися вокруг осей втулками. Кроме того, в проемах пластин закрепляются парные криволинейные призмы. Одна из ник закреплена на пластинах первого звена, вторая- на следующем. В ходе вращения призмы проворачивают друг друга, смягчая ударные нагрузки и осуществляя мягкий и плавный ввод в зацепление с зубьями звездочки и столь же плавный выход из этого зацепления. Такое решение позволяет снизить уровень воздушного шума, повысить скорость вращения.
Используют и конструкции с шарнирами скольжения. Они изнашиваются приблизительно вдвое быстрее, чем их аналоги, но обходятся заметно дешевле. В прорезях пластин вставлены специальные вкладыши, их скольжение по осям и обеспечивает поворот на необходимый угол. Применение вкладышей увеличивает площадь зацепления на 50%, повышая плавность хода, сокращая удары при разгоне и торможении и снижая уровень воздушного шума.
Для того, чтобы звенья не спадали с шестерен, используют направляющие, размещенные по центру цепи или же парные- по ее краям. Это такие же пластины, но без отформованных выступов и впадин. Если направляющие размещаются внутри, в зубьях делают соответственный пропил. Такая конструкция снижает прочность зубьев и, соответственно, скорость передачи и передаваемую мощность по сравнению с наружным расположением.
Зубчатые цепи благодаря мягкому и плавному зацеплению с шестернями создают самый низкий уровень шума среди подобных себе приводов. Их часто называют малошумными или бесшумными. Неограниченная ширина передачи позволяет создавать приводы шириной до 1,8 метра, предающие весьма значительные мощности. Если сравнить с роликовыми или втулочными, то сложность конструкции, вес и стоимость таких передач многократно выше. Это ограничивает их применение.
Фасоннозвенные цепи
Этот вид цепей изготавливают методом фасонного литья или горячей штамповки из стальной полосы. Крючковая разновидность имеет звенья, отформованные в виде единственной детали сложной формы. В зацепление звенья входят, если соединять их под углом около 60 о, а потом выпрямлять. Штыревая версия представляет собой отлитую из высококовкого чугуна деталь с отверстием, в которое вставляется стальной штырь и закрепляется шплинтом.
Такие приводы ограничены в скорости (до 3 м/сек) и в передаваемой мощности, зато не требуют сложных систем смазки и защиты от загрязнений. Неприхотливый привод широко применяется в сельхозмашинах, изношенные звенья с легкостью заменяются с применением обычного слесарного инструмента, в полевых условиях. Ремонтопригодность фасоннозвенных цепей существенно выше, чем у других типов.
Материал цепей
Все детали цепного механизма должны хорошо сопротивляться повышенным статическим и ударным нагрузкам, и быть достаточно износостойкими. Боковые пластины делают из высокопрочных сплавов, они работают в основном на растяжение. Оси, втулки, ролики, вкладыши и призматические элементы делаются из высокопрочных и хорошо цементируемых сплавов. Цементация проводится на глубину до 1,5 мм и обеспечивает хорошую стойкость к износу трением. После этого детали подвергаются термообработке закаливанием. Твердость доводится до 65 ед.
Зубчатые колеса делают из легированных сталей, также подвергаемых закалке до 60 ед.
Для передач малой скорости и мощности, при умеренных параметрах разгона и торможения применяют ковкие чугуны.
Для снижения шума и повышения плавности хода при ограниченных мощностях используют шестеренки из текстолита или прочных пластмасс. Применяют также наплавку металлических и нанесение полимерных покрытий на детали и узлы, работающие в агрессивных средах.
26 января 2022 года
группа 410
Предмет :"Техническая механика"
Тема занятия :"Достоинства и недостатки зубчатых передач"
Основные достоинства зубчатых передач:
- высокая нагрузочная способность;
- надежность работы в широком диапазоне скоростей и нагрузок;
- большая долговечность;
- постоянство передаточного отношения;
- высокий КПД.
Среди недостатков можно отметить:
- повышенные требования к точности изготовления;
- шум при высоких скоростях;
- высокую жесткость, не позволяющую компенсировать динамические нагрузки.
Отмеченные недостатки не снижают существенного преимущества зубчатых передач перед другими видами передач, что предопределяет их широкое применение в технике.
Группа 410
Предмет :"Техническая механика"
Тема занятий :"Виды, назначение зубчатых передач"
Зубчатые передачи: разновидности и принцип работы
Зубчатые передачи получили широкое распространение как в промышленном оборудовании, так и в бытовых приборах. Они служат промежуточным элементом между источником вращательно-поступательного движения и агрегатом, который является потребителем получаемой энергии. При этом передаваемая мощность может варьироваться от незначительных величин (например, в часовых механизмах) до огромных значений (в турбинах электростанций).
Принцип работы
В большинстве случаев генератор энергии и конечный агрегат имеют разные характеристики. Они отличаются по скорости вращения, мощности, углу приложения усилия. Чтобы обеспечить доставку крутящего момента от двигателя до конечного агрегата, необходимо использовать промежуточные модули, способные передавать усилие с минимальными потерями.
Такими модулями служат зубчатые колеса (шестерни). Они представляют собой диск с зубьями, расположенный на цилиндрической или конической поверхности. Обычно они используются парами разного диаметра с одинаковым количеством зубьев.
Во время работы механизма зубья двух шестерен сцепляются. Головка зуба входит в зацепление с повторяющим ее форму углублением на соседней шестерне. При проворачивании ведущего вала ведомый начинает вращаться в противоположную сторону.
Таким образом, вращающий момент передается от одного элемента к другому. Если диаметр ведущего колеса больше, то вращающий момент ведомого колеса уменьшается, и наоборот.
Основные виды зубчатых передач
В различных областях промышленности и приборостроения активно применяются все разновидности зубчатых передач. Ежегодно подобные механизмы производятся миллионными партиями. Сфера их использования настолько обширна, что найти прибор, в работе которого применяется вращательное движение без помощи зубчатых соединений, достаточно проблематично.
По конструктивному исполнению зубчатые передачи подразделяются на следующие категории:
- Цилиндирическая. Используется наиболее часто, так как имеет более простую относительно других типов технологию производства шестерен. Цилиндрическая зубчатая передача применяется для передачи крутящего момента между валами, которые находятся в параллельных плоскостях. Может иметь несколько форм зубьев: прямые, косые и шевронные. Данный вид передач нашел свое применение в двигателях внутреннего сгорания, коробках передач подвижных составов, станков, буров. Он широко распространен в металлургии, машиностроении и других сферах промышленности.
- Коническая. Получила свое название за счет необычной конструкции колесных пар. Имеет форму срезанного конуса, на котором нарезаны зубья. Величина профиля зубьев уменьшается от основания к вершине. Коническая зубчатая передача используется в сложных и комбинированных механизмах, для которых характерны частые изменения нагрузок и углов вращения. Примерами могут служить ведущие мосты автотранспорта, сельскохозяйственной техники или железнодорожных составов, приводы различных промышленных станков.
- Реечная. Используется для преобразования вращательного движения в поступательное, и наоборот. При этом одна из шестерен заменяется плоскостью с нарезанными зубьями. Реечная передача проста в производстве и установке, способна выдерживать значительные нагрузки. В основном она применяется в механизме станков, основанных на поступательном движении: прессы, транспортеры с попеременной подачей, рулевые механизмы управления в переднеприводных автомобилях.
Любой вид зубчатых передач отличается продолжительным эксплуатационным периодом и надежностью работы (при соблюдении определенного уровня нагрузки и своевременном обслуживании). Сравнительно небольшой механизм способен обеспечить высокий КПД, благодаря чему и применяется для широкого круга задач.
25 января 2022 года
Группа 410
Предмет :"Техническая механика с основами технологических измерений"
Тема занятия :"Способы изготовления резьб"
Основные методы создания резьбы следующие: 1 — нарезание резьбовыми резцами или резьбовыми гребенками; 2 — нарезание плашками, резьбонарезными головками и метчиками; 3 — накатывание при помощи плоских или круглых накатных плашек; 4 — фрезерование с помощью специальных резьбовых фрез; 5 — шлифование абразивными кругами.
21 января 2022 года
Группа 410
Предмет :"Техническая механика с основами технических измерений "
ВИДЫ РЕЗЬБОВЫХ СОЕДИНЕНИЙ
СОДЕРЖАНИЕ [скрыть]
Наиболее распространенным способом стыковки элементов различных конструкций является резьбовое соединение. Оно широко применяется в строительстве, при монтаже трубопроводов, в машиностроении и многих других отраслях. Популярность этого способа обусловлена следующими преимуществами:
- высокая надежность и продолжительный срок службы;
- создание разъемных соединений, простота монтажа и демонтажа при помощи общедоступных инструментов;
- контроль силы затягивания при сборке;
- малый вес и размеры крепежа, по сравнению с соединяемыми конструктивными элементами;
- широкая доступность, большой выбор типоразмеров крепежа.
Для использования при изготовлении и монтаже деталей необходимо знать существующие виды и параметры резьбовых соединений.
НАЗНАЧЕНИЕ И ВИДЫ РЕЗЬБОВЫХ СОЕДИНЕНИЙ
Резьбовые соединения любых видов резьб выполняют несколько основных функций. Основным назначением является обеспечение плотного соединения стыкуемых деталей с достижением необходимого значения. Кроме того, обеспечивается фиксация деталей в заданном положении, предотвращается возможность их смещения при эксплуатации конструкции или механизма. Еще одним распространенным назначением резьбовых соединений является обеспечение заданного расстояния между деталями.
Классификация соединений этого типа осуществляется по нескольким параметрам. При этом она имеет большое значение, поскольку от вида резьбовых соединений зависит их область применения, особенности эксплуатации, нормы отбраковки.
В зависимости от способа исполнения различают соединения, которые выполняются посредством крепежных элементов и непосредственные соединения. В первом случае монтаж выполняется при помощи болтов, шпилек, гаек, винтов и других вспомогательных элементов. Непосредственное соединение монтируется путем скручивания друг с другом соединяемых элементов, например, труб с нарезанной резьбой.
В зависимости от формы поверхности различают цилиндрические и конические резьбы. Оба этих типа резьб могут быть наружными и внутренними. По направлению витков нарезка может быть левой или правой.
Ключевым параметром для классификации является тип профиля нарезки. По этому признаку выделяют следующие виды резьбовых соединений деталей:
- метрическая;
- дюймовая;
- трубная цилиндрическая;
- трапецеидальная;
- упорная;
- круглая.
Рассмотрим эти типы более подробно.
МЕТРИЧЕСКАЯ РЕЗЬБА
Самым распространенным видом резьбовых соединений является метрическая резьба. Ее профиль выполняется в соответствии с ГОСТ 9150-81 в форме равностороннего треугольника с углом 60°. Шаг метрической резьбы может составлять 0,25-6 мм, а внешний диаметр — от 1 мм до 600 мм. Такой тип резьбового соединения применяется при изготовлении большинства крепежных деталей.
Кроме того, применяется коническая метрическая резьба с диаметром 6–60 мм конусностью 1:16. Этот тип нарезки позволяет выполнять герметичные соединения. При ее использовании достигается стопорение крепежа, что исключает необходимость применения стопорных гаек.
ДЮЙМОВАЯ РЕЗЬБА
Дюймовая резьба имеет профиль в форме равнобедренного треугольника со значением угла 55°, что отличает ее от формы профиля метрической нарезки. Диаметры резьбы измеряются в дюймах. Шаг определяется в количестве витков на 1 дюйм длины резьбовой части изделия. В промышленности применяются резьбовые соединения с наружным диаметром от 3/16 до 4 дюймов с числом витков на один дюйм от 3 до 28. Этот тип нарезки широко применяется на деталях трубопроводов, а также на крепеже производства США, Великобритании и ряда других стран.
Также выпускаются изделия с конической дюймовой резьбой. Благодаря конической форме достигается улучшенная герметичность соединения, что позволяет не использовать уплотнительные элементы. Коническая дюймовая нарезка широко применяется при прокладке напорных трубопроводов малого диаметра в гидравлических системах.
ТРУБНАЯ РЕЗЬБА
Трубная цилиндрическая резьба выполняется по ГОСТ 6357-81. Она имеет профиль в форме равнобедренного треугольника, угол наклона гребней составляет 55°. Верхние грани гребней скруглены. Благодаря этому устраняются дополнительные зазоры в зоне выступов и впадин, что обеспечивает повышенную герметичность соединения. Трубная резьба относится к дюймовым. Ее диаметр составляет от 1/16 до 6 дюймов, а шаг — от 11 до 28 витков.
По сравнению с другими видами дюймовых резьб шаг трубной резьбы сокращен. Уменьшенный шаг позволяет не допустить критического сокращения толщины стенки трубы, что необходимо для сохранения прочностных характеристик трубопровода.
Трубная резьба может быть цилиндрической и конической. В последнем случае ее конусность определяется соотношением 1:16.
ТРАПЕЦЕИДАЛЬНАЯ
К резьбовым соединениям этого вида относятся чаще всего соединения типа винт-гайка. Трапецеидальная резьба выполняется в соответствии с ГОСТ 9481-81. Ее форма представляет собой равнобокую трапецию. Угол наклона граней составляет 30°. Для резьбы крепежных элементов, применяемых в червячных передачах, предусмотрен угол наклона 40°.
Трапецеидальный профиль резьбы позволяет достичь повышенной прочности соединения. Благодаря этому ее применяют для соединения деталей механизмов, работающих под воздействием динамических нагрузок, например, в ходовых гайках, которыми фиксируются штоки задвижек и т. д.
УПОРНАЯ РЕЗЬБА
Упорная резьба в соответствии с ГОСТ 10177-82 имеет профиль в виде неравнобокой трапеции. Угол наклона одной грани гребня составляет 3°, а второй грани — 30°. Этот тип применяют для крепежных элементов диаметром от 10 мм до 600 мм. Шаг резьбы составляет 2–25 мм. Этот вид резьбового соединения используется для крепления деталей, которые в процессе эксплуатации испытывают значительные осевые нагрузки в одном направлении. Профиль нарезки позволяет эффективно противостоять таким нагрузкам.
КРУГЛАЯ РЕЗЬБА «ЭДИСОНА»
Круглая резьба, выполняемая в соответствии с ГОСТ 6042-83, имеет профиль, формируемый дугами. Угол наклона сторон составляет 60°. Благодаря такой форме профиля круглая резьба обладает высокой стойкостью к механическому износу. Это позволяет применять ее в деталях конструкций и механизмов, которые подвержены регулярным переменным нагрузкам, например, в деталях трубопроводной арматуры.
21 января 2022 г
Группа 410
Предмет :"Техническая механика с основами технических измерений"
Тема занятия :"Достоинства и недостатки заклепочных соединений"
ЗАКЛЕПОЧНЫЕ СОЕДИНЕНИЯ: ДОСТОИНСТВА И НЕДОСТАТКИ
СОДЕРЖАНИЕ [скрыть]
Заклепочное соединение деталей получило широкое применение в строительстве, машиностроении, приборостроении и многих других отраслях. Заклепки — это широкая категория метизов, которые позволяют создавать прочные и жесткие неразъемные соединения. Монтажные узлы рассчитаны на высокую долговечность при значительных эксплуатационных нагрузках. Разберем основные особенности, достоинства и недостатки заклепочных соединений.
ЗАКЛЕПОЧНОЕ СОЕДИНЕНИЕ — ОСОБЕННОСТИ СТРОЕНИЯ
Заклепочные соединения относятся к неразъемным соединениям, которые используются для сопряжения элементов конструкций из разных материалов. Как правило, они служат для скрепления деталей из листового металла. Заклепочное соединение состоит из двух или более сопрягаемых деталей и заклепки, которая создает усилия, удерживающие вместе соединительные элементы. Заклепка вставляется в соосные монтажные отверстия, выполненные в сопрягаемых изделиях методом сверления или продавливания. Метод выполнения отверстий выбирают в зависимости от материала деталей и их толщины.
Заклепка состоит из следующих частей:
- стержень круглого сечения;
- закладная головка, выполненная в процессе изготовления крепежного элемента;
- замыкающая головка, которые формируется в процессе клепки.
Это классическая конструкция простой заклепки, которая имеет широкое применение. Также для монтажа отдельных узлов разработано значительное число видов заклепочного крепежа. Для изготовления заклепок сегодня используются специальные высадочные автоматы. Стержень заклепки может быть сплошным или иметь сквозное отверстие.
Клепка производится вручную при помощи специального инструмента, либо при помощи пневматических клепальных молотков и прессов. Часто для соединения деталей используется много заклепок, установленных по единой оси. Такое соединение называют заклепочным швом.
МАТЕРИАЛ ИЗГОТОВЛЕНИЯ
Устойчивость, надежность, прочность заклепочного соединения определяются в значительной степени материалом заклепки. Также от него зависит удобство и эффективность монтажа, необходимость применения дополнительного инструмента или оборудования. В большинстве случаев для изготовления заклепок используют низкоуглеродистые марки стали, медь, алюминий, некоторые другие виды цветных металлов и сплавов.
Учитывая особенности заклепочных соединений, материал заклепки должен отвечать таким основным требованиям:
- достаточный уровень пластичности для выполнения клепки;
- сопоставимый коэффициент температурного расширения с материалов соединяемых элементов — позволяет исключить возникновение дополнительных напряжений, которые приводят к износу и разрушению соединительного узла;
- однородный химический состав с материалов соединяемых деталей (сталь-сталь, алюминий-алюминий, медь-медь и т. д.) — предотвращает образование гальванических токов, которые приводят к интенсивной коррозии металлов.
Правильный подбор материала заклепки, наряду с соблюдением технологии монтажа и подбором размерных характеристик крепежа, является важным условием долговечности и надежности соединения.
Материал прямо влияет на технологию монтажа заклепочных соединений. Клепка с применением стальных заклепок диаметром не более 10 мм, а также крепежных элементов из меди, алюминия, латуни, других легких сплавов производится холодным способом. Монтаж соединений из стальных заклепок диаметром свыше 10 мм выполняют горячим способом, чтобы добиться нужной пластичности металла.
ВИДЫ ЗАКЛЕПОЧНЫХ СОЕДИНЕНИЙ
В промышленности и строительстве применяется множество видов заклепок и выполняемых с их помощью соединений. Классификация заклепочных соединений предусмотрена по следующим основным критериям:
- Функциональное назначение.
- Конструкция шва.
- Количество срезов.
- Количество рядов заклепок.
- Форма закладных головок.
- Форма стержня.
По функциональному значению выделяют прочные, плотные и комбинированные типы заклепочных соединений. Прочные соединения рассчитаны на удержание эксплуатационных нагрузок. Плотные — поддерживают герметичность соединительного узла. Комбинированные заклепки и заклепочные соединения совмещают эти функции.
По конструкции соединительного шва различают соединения со швом внахлест и встык. Наиболее распространен первый тип. При монтаже шва внахлест используются специальные накладки.
По числу линий среза, которые проходят через стержень заклепки под действием эксплуатационных нагрузок различают односрезные и многосрезные разновидности заклепочных соединений. Для многосрезных типов количество линий среза не ограничивается.
По количеству заклепочных рядов различают однорядные, двухрядные, трехрядные и т. д. соединительные узлы. Общее число рядов не ограничено нормативными требованиями.
В зависимости от формы закладных головок бывают такие виды заклепок и заклепочных соединений:
- полукруглые;
- цилиндрические;
- полупотайные;
- потайные и т. д.
Еще один важный критерий — форма и конструкция стержня заклепки. Стержни могут быть:
- сплошные — традиционный тип стержня без отверстия;
- пустотелые — в теле стержня заклепки выполнено сквозное отверстие;
- полупустотелые — стержень разделен на две половины, в одной из которых выполнено отверстие, а вторая является сплошной.
Основным нормативным документом, регламентирующим виды заклепочных соединений способы их выполнения, а также их размерные характеристики, является ГОСТ 10303-68. Кроме этого действует несколько других ГОСТов, регулирующих эту сферу.
ГДЕ ПРИМЕНЯЮТСЯ ЗАКЛЕПОЧНЫЕ СОЕДИНЕНИЯ?
Использование заклепок долго оставалось наиболее распространенным способом монтажа неразъемных соединений до того, как развитие сварочных технологий вышло на достаточно высокий уровень. Однако и сейчас применение заклепочных соединений распространено во многих отраслях. Как правило, с их помощью соединяют детали конструкций из листовых материалов — стали, цветных металлов, пластика и т. д. Заклепки большого диаметра используют для соединения элементов профильного металлопроката — швеллера, двутавровых балок, уголка и других.
Заклепки создают прочные соединительные узлы с повышенной устойчивостью к вибрационным нагрузкам. Поэтому основными направлениями, где применяются в основном заклепочные соединения являются те сферы, в которых ответственные конструкции регулярно подвергаются воздействию вибрации и повторных нагрузок. В том числе их используют в автомобилестроении, авиастроении, судостроении, приборостроении и других отраслях.
Кроме этого, в машиностроении и строительстве заклепочные соединения применяют в тех случаях, когда нельзя использовать сварку:
- материалы соединяемых деталей нельзя сваривать друг с другом;
- при сварке существует опасность коробления поверхности;
- использование сварки может привести к отпуску деталей, прошедших термическую обработку;
- использование сварки затруднено по конструктивным причинам или из-за особых условий выполнения монтажных работ.
Существует большое число разновидностей клепальных соединений, которые получили распространение в отдельных отраслях, при монтаже разных конструкций.
ДОСТОИНСТВА И НЕДОСТАТКИ ЗАКЛЕПОЧНОГО СКРЕПЛЕНИЯ
Как и любой вид крепежных элементов, заклепки имеют свои плюсы, благодаря которым область применения заклепочных соединений остается достаточно широкой, и недостатки, ограничивающие их использование. Разберем их основные достоинства и недостатки.
ДОСТОИНСТВА ЗАКЛЕПОЧНЫХ СОЕДИНЕНИЙ
Среди основных достоинств заклепочных соединений можно назвать такие преимущества:
- простота технологического исполнения соединительных узлов — не требуется высокая квалификация персонала, выполняющего монтажные работы;
- возможность монтажа сложных узлов — заклепки позволяют соединять две и более детали из разных конструкционных материалов;
- возможность соединения несвариваемых и разнородных материалов;
- отсутствие термического воздействия на материалы соединяемых деталей при выполнении монтажа — технология позволяет соединять элементы, для которых недопустимо использование сварки;
- высокий уровень надежности, длительный срок службы монтажного узла;
- повышенная устойчивость к вибрационным и повторным нагрузкам — возможность монтажа ответственных конструкций, эксплуатируемых в сложных условиях.
Благодаря этим достоинствам заклепочные соединения остаются актуальным способом монтажа конструкций, несмотря на имеющиеся альтернативные технологии.
НЕДОСТАТКИ ЗАКЛЕПОЧНЫХ СОЕДИНЕНИЙ
В то же время существуют характерные недостатки заклепочных соединений, в результате которых их применение существенно сокращено.
Основные минусы:
- повышенная материалоемкость — на заклепки требуется повышенный расход металла, что увеличивает стоимость монтажа;
- повышенная трудоемкость монтажных работ в связи с необходимостью выполнения соединения в сборе;
- необходимость использования специального клепального инструмента;
- необходимость горячего способа монтажа для стальных заклепок большого диаметра;
- ослабление конструкции и создание дополнительных напряжений при большом количестве отверстий под заклепки;
- деформация заклепочного соединения и быстрое разрушение при неправильном диаметре отверстия.
В связи с этими недостатками заклепочные соединения применяют редко, если имеется возможность выполнить монтаж конструкции при помощи сварки или резьбового крепежа.
20 января 2022 года
Группа 410
Предмет :"Техническая механика с основами технических измерений"
Тема занятия :"Назначение, конструкция, применение заклепочных соединений"
"Классификация заклепочных соединений"
8 Конструкция, классификация и область применения заклепочных соединений
8. Конструкция, классификация и область применения заклепочных соединений. Разновидности заклепок, материалы, применяемые для изготовления заклепок.
Заклепочное соединение неразъемное. Применяют для соединения листов и фасонных прокатных профилей. Соединение образуют расклепыванием стержня заклепки, вставленной в отверстие деталей. При расклепывании вследствие пластических деформаций образуется замыкающая головка, а стержень заклепки заполняет зазор в отверстии. Силы, вызванные упругими деформациями деталей и стержня заклепки, стягивают детали. Отверстия в деталях продавливают или сверлят. Сверление менее производительно, но обеспечивает повышенную прочность. Клепку можно производить вручную или машинным способом. Стальные заклепки малого диаметра и заклепки из цветных металлов ставят без нагрева- холодная клепка. Стальные заклепки диаметром больше 10 мм ставят горячим способом- горячая клепка. В зависимости от конструкции соединения применяют различные типы заклепок: с полукруглой головкой, полупотайная, потайная, трубчатая.
По назначению заклепочные соединения разделяют на прочные(в металлоконструкциях), прочноплотные(в котлах и резервуарах с высоким давлением), плотные(в резервуарах с небольшим внутренним давлением).
По конструктивному признаку различают заклепочные соединения внахлестку и встык, однорядные и многорядные, односрезные и многосрезные.
Заклепочные соединения применяют для деталей, материал которых плохо сваривается, и в тех конструкциях, где важно растянуть во времени развитие процесса разрушения.
Заклепки изготовляют из стали, меди, латуни, алюминия и других металлов. Материал заклепок должен обладать пластичностью и не принимать закалки. При выборе материала для заклепок необходимо стремиться к тому, чтобы температурные коэффициенты линейного расширения заклепок и соединяемых деталей были равными или близкими.
Допускаемые напряжения для заклепок зависят в основном от характера обработки отверстия(продавленные или сверленные) и характера внешней нагрузки(статическая, динамическая).
20 января 2022 года
Группа 410
Предмет :"Техническая механика с основами технических измерений"
Тема занятия :"Обозначение муфт на чертежах"
Чертеж муфты
Муфта - это трубопроводное соединение с элементами для соединения и уплотнения частей трубопровода.
Чертеж муфты выполняется на основании - единая система конструкторской документации (ЕСКД).

Вы можете бесплатно скачать этот простой чертеж для использования в любых целях. Например для размещения на шильдике или наклейке.
Как начертить чертеж:
Начертить чертеж можно как на листе бумаги, так и с использованием специализированных программ. Для выполнения простых эскизных чертежей особых инженерных знаний не требуется.
20 января 2022 года
Группа 410
Предмет :"Техническая механика с основами технических измерений"
Тема занятия :"Назначение и классификация муфт"
Муфты: классификация, виды, назначение
Муфта – устройство, предназначенное для соединения концов валов или для соединения валов с расположенными на них деталями.
Основное назначение: передача вращающего момента без изменения его модуля и направления. Функции, выполняемые муфтами: предохранение механизма от перегрузок, компенсирование несоосности валов, разъединение или соединение валов во время работы и др.
В зависимости от конструкции муфты различаются по функциональному назначению и принципу действу. Различают следующие виды муфт: механические, гидравлические, электрические и др. Широко применяемые муфты стандартизованы. Основная паспортная характеристика муфты - значение вращающего момента, на передачу которого она рассчитана. Ниже рассматриваются только наиболее распространенные в машиностроении механические муфты.
По характеру соединения валов муфты подразделяют на неуправляемые (постоянные), управляемые и самоуправляемые (автоматические).
Виды муфт
Муфта глухая образует жесткое и неподвижное соединение валов. Они не компенсируют ошибки изготовления и монтажа, требуют точной центровки валов. Применяются обычно глухие муфты для тихоходных валов.
Втулочная муфта – самая простая из глухих муфт, состоит из соединительной втулки со штифтами или шпонками. Основное их достоинство – простота конструкции. Применяют их при относительно небольших нагрузках на валах диаметрами до 60…70 мм.
Муфта фланцевая – наиболее распространенная, состоит из двух полумуфт 2, соединенных болтами 1. Болты ставят через один: с зазором (вариант I) и без зазора под развертку (вариант II). Центрирование полумуфт в этом случае осуществляют болтами, установленными без зазора, которые рассчитывают на срез. Установка болтов без зазора позволяет получить муфты меньших габаритов и поэтому более распространена.
Фланцевые муфты применяют для соединения валов диаметром до 200 мм и более. Достоинствами таких муфт являются простота конструкции и сравнительно небольшие габариты.
Жесткая компенсирующая муфта. За счет подвижности деталей такие муфты компенсируют радиальные, угловые и осевые смещения валов, вызванные неточностями их изготовления, монтажа и упругими деформациями. Это позволяет уменьшить нагрузки на валы и подшипники.
Недостаток жестких компенсирующих муфт – отсутствие упругодемпфирующих элементов, смягчающих толчки и удары. Наибольшее распространение получили кулачково-дисковая и зубчатая.
Кулачково-дисковая муфта состоит из двух полумуфт 1 и 3, соединенных промежуточным диском 2. При работе диск перемещается по пазам полyмуфт, и тем самым компенсируются несоосность соединяемых валов (радиальные смещения – до 0,04d, угловые – до 30').
Скольжение выступов в пазах сопровождается их износом. Интенсивность износа возрастает с увеличением несоосности и частоты вращения. Для уменьшения износа поверхности трения муфты периодически смазывают и не допускают на них больших напряжений смятия.
Из условия износостойкости кулачково-дисковых мyфт рассчитывают давление на боковых поверхностях выступов и пазов: , (7.1) где Тр – расчетный вращающий момент; h – рабочая высота выступа; D, d – соответственно наружный и внутренний диаметры; [p] – допускаемое давление: при термически необработанных, хорошо смазываемых поверхностях или при закаленных поверхностях трения [p] = 15…30 МПа.
Детали кулачково-дисковых муфт изготовляют из сталей Ст5 (поковка) или 25Л (литье). Для тяжелонагруженных муфт применяют легированные стали типа 15Х, 20Х с цементацией рабочих поверхностей.
Зубчатая муфта состоит из двух полумуфт 1 и 3 с наружными зубьями эвольвентного профиля и разъемной обоймы 2 с внутренними зубьями. Передача вращающего момента осуществляется большим числом одновременно работающих зубьев, что обеспечивает высокую нагрузочную способность и малые габариты муфты.
Для компенсации смещений деталей предусматривают торцевой зазор δ. Для ослабления вредного влияния кромочного контакта применяют зубья бочкообразной формы, а соединение выполнено с увеличенными зазорами. Зубчатые муфты допускают угловое смещение валов Δα max = 1,5°, радиальное Δr = 0,2…0,6 мм, осевое (на рисунке не показано) – 1…8 мм.
Детали зубчатых муфт изготовляют из углеродистых сталей типа 45, 40Х, 45Л коваными или литыми. Для повышения износостойкости зубья полумуфт подвергают термической обработке до твердости не ниже 40НRC, а зубья обойм – не ниже 35HRC.
Упругие компенсирующие муфты применяются не только для компенсации смещения валов, но и для снижения динамичности нагрузок и амортизации колебаний, возникающих при работе передач машин.
Муфта упругая втулочно-пальцевая состоит из двух полумуфт 1, соединенных пальцами 2, на которые для смягчения ударов надеты гофрированные резиновые втулки. Такие муфты в силу простоты конструкции получили широкое применение в приводах от электродвигателей для валов диаметрами 9…160 мм при вращающих моментах 6,3…16000 Нм.
Толщина резиновых втулок невелика, и поэтому амортизирующая способность муфты незначительна. Они допускают радиальное смещение валов до 0,6 мм, продольное – до 5 мм, угловое – до 1°. Для ограничения износа среднее контактное давление пальца на втулку находят по формуле: где z = 6 – число пальцев; Dm – диаметр окружности расположения осей пальцев; dп – диаметр пальцев; l – длина упругого элемента; [p] ≈ 2 МПа – допускаемое давление для резиновых втулок.
Муфта со змеевидными пружинами состоит из двух полyмуфт 1 с зубьями специальной формы, между которыми свободно расположены секции змеевидной пружины 3 прямоугольного сечения. Кожух 2, состоящий из двух половин, служит резервуаром для пластичного смазочного материала и предохраняет пружину от выпадения.
Муфта используется для передачи больших вращающих моментов, обладает хорошими эксплуатационными качествами, имеет небольшие габариты, но сравнительно дорогостоящая. В зависимости от размеров муфты могут компенсировать радиальные смещения валов 0,5…3 мм, осевые – 4…20 мм и угловые до 1°15'.
Материалы полумуфт – сталь 45, стальное литье 45Л; пружин – пружинные стали 65Г, 60С2. Расчет муфты предусматривает проверку прочности пружины при изгибе методами сопротивления материалов.
Управляемые (сцепные) муфты Позволяют соединять и разъединять валы без остановки двигателя. По конструкции управляемые муфты можно разделить на кулачковые, зубчатые, основанные на зацеплении, и фрикционные, основанные на трении. Кулачковые и зубчатые муфты имеют весьма небольшие габариты и массу, не допускают проскальзывания. Однако их включение на ходу сопровождается ударами. Фрикционные муфты позволяют плавно соединять ведущий и ведомые валы под нагрузкой при любой скорости их вращения, предохраняют механизмы от внезапных перегрузок. Управляемые муфты требуют точной соосности соединяемых вaлов.
Кулачковая муфта состоит из двух полумуфт 1 и 2, имеющих на сцепляемых торцах выступы – кулачки. При включении муфты кулачки одной полумуфты входят во впадины другой, создавая жесткое соединение.
Включение кулачковой муфты во избежание ударов производят при остановленном двигателе или с малыми скоростями (до 1 м/с). Полумуфты чаще всего располагают на одном валу, что обеспечивает хорошую их соосность. При выключенной муфте зубчатое колесо свободно вращается на подшипнике скольжения 3. Если муфта включена, вращающий момент от зубчатого колеса передается через кулачки и шлицы на вал.
Для устранения ударов и шума при включении муфты применяют специальные соединительные устройства – синхронизаторы. Кулачковые муфты изготовляют из сталей 20, 15Х, 20Х с последующей цементацией или сталей 40Х, 30ХН с последующей объемной закалкой. Размеры муфт принимают конструктивно, а затем выполняют проверочный расчет кулачков на износостойкость и прочность.
Фрикционные сцепные муфты передают вращающий момент между полумуфтами за счет сил трения на рабочих поверхностях.
Фрикционные муфты: а – однодисковая; б – многодисковая; в – конусная
В начальный период касания полумуфт происходит относительное проскальзывание их рабочих поверхностей (смазанных или сухих), и тем самым обеспечивается плавность включения муфты. При установившемся движении проскальзывание не происходит, а при перегрузке муфта пробуксовывает, что предохраняет машину от поломок. Фрикционные муфты должны обладать надежностью сцепления, высокой износостойкостью и теплостойкостью контактирующих поверхностей. Материал трущихся деталей (накладок) выбирается в зависимости от среднего контактного напряжения (давления): , (7.3) где Fa – осевая сила; Т – вращающий момент; k = 1,3…1,5 – коэффициент запаса сцепления; Dm – средний диаметр контакта; f – коэффициент сцепления (трения покоя); z – число пар поверхностей трения; А = πDmb – площадь поверхности трения; b – ширина поверхности трения; [p] – допускаемое контактное напряжение. По формуле (7.3) может быть рассчитан вращающий момент, который может передавать фрикционная муфта. Для увеличения передаваемого вращающего момента можно увеличить число пар поверхностей трения. Многодисковые фрикционные муфты имеют небольшие габариты и не требуют большого усилия для их включения.
Самоуправляемые автоматические муфты выполняют автоматически одну из следующих функций: ограничение передаваемой нагрузки – предохранительные муфты; передачу нагрузки (момента) только в одном направлении – муфта обгона; включение и выключение при заданной скорости – центробежные муфты.
Предохранительную муфту срабатывают, когда вращающий момент превышает некоторую установленную величину. При достижении вращающим моментом предельной величины под действием осевых усилий, обусловленных формой впадин полумуфты, шарики смещаются в осевом направлении (преодолевая сопротивление пружины) и размыкают муфту с последующим прощелкиванием.
Муфта обгона (мyфты свободного хода) предназначены для передачи вращающего момента только в одном направлении. Наибольшее распространение получили фрикционные обгонные мyфты, передающие вращающий момент за счет заклинивания между полумуфтами промежуточных тел (в основном роликов). Такие муфты бесшумны, компактны, могут работать при высокой частоте вращения. Их изготовляют для вaлов диаметром 10…90 мм и передачи момента до 750…800 Нм. Обгонные роликовые муфты применяют в приводах агрегатов двигателя самолета (например, в приводах стартер-генераторов) и в приводах несущих винтов вертолетов; при отказе одного двигателя движение винта не тормозится, так как обгонная муфта позволяет зубчатым колесам вращаться. При отказе обоих двигателей обгонные муфты не препятствуют вращению несущего винта в режиме авторотации.
Пусковую (центробежную) муфту используют для плавного пуска приводов грузоподъемных машин конвейеров и т.п. Они позволяют электродвигателю легко разогнаться и по достижении им определенной скорости начать плавный разгон рабочего органа. Одновременно пусковые мyфты выполняют и предохранительные функции. Распространены колодочные и дисковые центробежные фрикционные муфты. Центробежную муфту устанавливают на вал электродвигателя. При наличии ременной передачи от электродвигателя к рабочему органу наружную ведомую часть муфты конструируют в виде шкива.
Комментариев нет:
Отправить комментарий